 |

Roofing With Concrete Tile
Our roofing company is located in Southern California, where most houses are
roofed with concrete tiles. Until 30 or 40 years ago, almost all roof tiles
installed in the United States were clay tiles, like those used for thousands
of years in Europe and China. In the past few decades, though, concrete roofing
tiles have edged out clay on residential roofs and now dominate the market.

Roof tiles, whether concrete or clay, are very resistant to fire. Although some
traditionalists prefer clay tiles over concrete, there is no arguing with the
main advantage of concrete tiles: They cost about half as much as clay (see
"Concrete Tile vs. Clay Tiles," below).
Concrete Tile vs. Clay Tile
The main advantage of concrete tiles over clay tiles is their lower cost.
Proponents of clay tiles usually mention two advantages of clay over concrete
tiles: better colorfastness and longer physical durability.
Colorfastness. The color of a clay tile
is not affected by exposure to the elements; the same cannot be said of
concrete tiles. Although most concrete roof tiles are manufactured with
an integral pigment that colors the entire thickness of the tile, the
color of concrete tiles will fade over time. "Concrete tile will never
hold its color as well as clay," says Ken McGee, owner of The Tile Man,
a supplier and installer of concrete and clay roof tiles in Louisburg,
N.C.
Durability. Well-made concrete tiles
should last a long time, although probably not as long as clay tiles;
estimates range from 30 to 50 years. By contrast, many European clay tile
roofs are still waterproof after a century of service. Traditional fired
clay, although relatively easy to break, does not degrade from exposure
to the elements. Because objects made from fired clay can't burn or rot,
they are among the most durable objects known to archeology. Clay objects
can easily last for thousands of years.
Although some early concrete roof tiles had durability problems, especially
in areas with frequent freeze/thaw cycles, most concrete roofing tile
manufacturers claim that today's concrete tiles are more consistent and
durable than ever. Although there are reports of isolated cases of seriously
deteriorated concrete roof tiles, tile manufacturers claim that such problems
are rare and occur only when a bad batch of tiles gets through their quality-control
systems.
"A few years ago, I saw a job up in the mountains where the concrete tile
just disintegrated in the winter," says McGee. "It just fell apart. But
that was unusual. Most of the manufacturers are very careful. I wouldn't
let anyone knock concrete too much. You don't have to worry about concrete
tile falling apart any more."
Martin Holladay
|
Consider the Weight
Standard-weight concrete roof tiles generally weigh between 9 1/2 and 12 pounds
per square foot significantly more than asphalt shingles, which weigh
only 2 1/2 to 4 pounds per square foot. For houses where weight is a concern,
many tile manufacturers offer lightweight roof tiles weighing 5 1/2 to 7 pounds
per square foot. These tiles are made with a lightweight aggregate, like expanded
shale, instead of sand.
If you're reroofing a house with existing asphalt shingles and you're not sure
whether the roof structure is adequate to support concrete tiles, you should
have the roof framing checked by an engineer before proceeding.
Tile Types
Concrete roof tiles are available in three basic profiles: mission S-tiles (or
"Spanish S"), villa tiles (low-profile tiles with a double-S shape), and flat
tiles, which are often designed to look like wood shakes or slates.
The job shown in this article used 17-inch-long Spanish S-tiles made by Eagle
Roofing Products (see "Sources of Supply," page 4 of article). These S-tiles
lock together along the sides, where they form a lap joint.
Tile manufacturers provide trim tiles specifically designed to complement their
various tile profiles. Most roofs will require at least two different types
of tile: standard field tiles and ridge tiles. For jobs using S-tiles, we trim
the ridges, hips, and rakes with a simple barrel trim tile. Some styles of roof
tile use a rake trim tile that differs from the ridge tiles. Some manufacturers
also offer a "hip starter" tile, a trim tile designed to be installed as the
bottom tile on a hip.
Low-slope installations. In general, the minimum
slope for a tile roof is 3/12. If a customer insists on installing roof tiles
on a roof with a pitch below 3/12, consult the tile manufacturer for installation
specifications. Low-slope applications will require a carefully detailed waterproof
membrane (for example, a self-sticking bituminous membrane) under the tiles.
In addition, many tile manufacturers require that tiles on a low-slope roof
be installed using a method that minimizes the number of fasteners that penetrate
the membrane.
With or without battens? Concrete roof tiles
can be either installed on battens parallel to the eaves or direct nailed to
the felt-covered plywood or OSB sheathing. Here in San Diego, we have had excellent
success direct nailing concrete roof tiles.
Most tile manufacturers permit direct nailing, except on roofs with a pitch
steeper than 7/12 or in very cold climates subject to ice dams.
When battens are used, they are typically 1x2s, with one course of battens for
each course of tiles. It's important to leave a gap of about an inch between
the ends of adjacent battens, in order to allow a gap for water to drain. Battens
should be no longer than 48 inches, for the same reason.
Necessary tools. The three most important
tools for installing concrete roof tiles are a nail gun, a gas-powered cut-off
saw or circular saw with a diamond blade, and a leaf blower for cleaning off
the dust.
Prepping the Job
Roof tiles are not completely waterproof; in a driving rain, some water is likely
to get past them. We install the asphalt felt carefully, because it is the most
important waterproof layer on a tile roof.
Forty-pound felt. Tile manufacturers require,
at a minimum, a single layer of #30 asphalt felt. Because a heavier felt is
more durable and holds up better to foot traffic during tile installation, we
always use #40 asphalt felt. The felt should be installed with a minimum 2-inch
head lap and 6-inch side lap.
To avoid leaks at the sides of dormers, chimneys, and skylights, we carefully
crease the felt and turn it up, rather than cutting it on the sheathing. For
extra protection, we often use a peel-and-stick flashing membrane at penetrations
such as roof vents, or at tricky areas around chimneys and skylights.
On tile roofs, all plumbing vent pipes get two layers of flashing. The primary
flashing, a galvanized steel boot with a minimum skirt width of 6 inches, is
installed at the same time as the asphalt felt. This flashing is bedded in asphalt
roofing cement and is installed on top of one course of the asphalt felt, while
the next felt course laps over the flashing (see Figure 1).
|
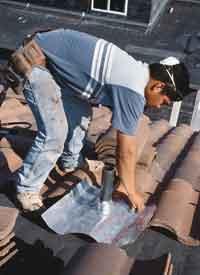 |
Figure 1. Each plumbing vent
receives two layers of metal flashing. The primary flashing is galvanized
and is installed at the same time as the asphalt felt (left). The secondary
flashing is installed later, when the tiles go on. An S-tile roof gets secondary
flashings made of aluminum, which is flexible enough to conform to the curve
of the tiles (right). |
While workers are on the roof, it's possible to get a few unintended holes or
rips in the felt. Because the felt, rather than the tiles, is the roof's waterproof
layer, we're always careful to patch all such tears and holes with felt, roofing
cement, or a high-quality caulk.
Ridge boards and hip boards. Concrete tile
roofs require special nailers at ridges and hips. These nailers ridge
boards and hip boards are lengths of 2-by lumber, installed on edge.
The height of these nailers varies, depending on the configuration of the tiles
being installed. The most common sizes used are 2x3s, 2x4s, and 2x6s (Figure
2). The ridge and hip boards are usually toe-nailed in place after the roof
is felted and then individually wrapped with additional pieces of felt.
|
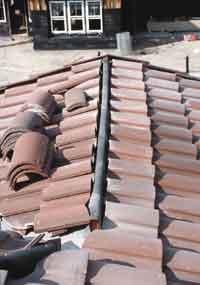 |
Figure 2. Typically, hip boards
nailers that support the hip shingles are 2x4s or 2x6s (left).
Hip and ridge boards are installed after the roof has been felted and are
later separately wrapped with felt (right). |
by Fred Martin
This article has been provided by www.jlconline.com. JLC-Online is produced by the editors and publishers of The Journal of Light Construction, a monthly magazine serving residential and light-commercial builders, remodelers, designers, and other trade professionals.
|
 |